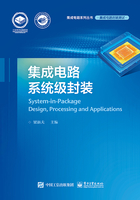
3.2.4 高密度结构设计
高密度系统级封装是一种非常广泛的概念,按芯片间信号互连方式可以分为焊线互连封装结构、倒装互连封装结构、焊线互连和倒装互连的混合封装结构;按内部集成的传感器、MEMS、无源元器件等可分为集成芯片和元器件的常规封装结构、传感器封装结构;按芯片贴装位置可分为采用芯片堆叠的封装结构、3D封装结构、双面封装结构、采用埋入式基板的嵌入式封装结构等,如图3-28~图3-34所示。

图3-28 焊线互连封装结构

图3-29 倒装互连封装结构

图3-30 焊线互连和倒装互连的混合封装结构

图3-31 传感器封装结构

图3-32 3D封装结构

图3-33 带屏蔽功能的双面封装结构

图3-34 采用埋入式基板的嵌入式封装结构
随着各种新技术、新材料、新工艺的不断发展,各种高密度封装应运而生,下面重点介绍各种高密度封装的结构和设计。
1. 2D高密度结构设计(2D High Density Structure Design)
2D高密度结构设计取决于芯片封装集成密度、芯片数量,以及芯片和元器件的集成。随着近年来芯片级封装(Chip Scale Package,CSP)、多芯片模块(Multi-Chip Module,MCM)等的高速发展,体积小、密度高、功能多、成本低、可靠性高已成为微电子封装产品的发展趋势。
CSP技术可以有效提高封装密度。CSP通常指封装外形的尺寸小于或等于1.2倍裸芯片尺寸的先进封装形式,具有体积小、I/O端口较多、电性能好、热性能好等特点。最具代表性的CSP是晶圆级芯片封装(Wafer Level Chip Scale Packaging,WLCSP),可通过两种途径实现2D高密度结构:采用更高制程的工艺,降低芯片中线路的宽度和间距,从而将芯片尺寸进一步缩小;通过采用更小的球径和球间距的方式,极大缩小封装尺寸。例如,将锡球间距e从1.5mm缩小到0.4mm,锡球尺寸b从0.75mm缩小到0.25mm,以225个I/O端口为例,WLCSP尺寸可以从12mm×12mm缩小至6.5mm×6.5mm,封装面积可以大幅缩小70%,如图3-35所示。

图3-35 WLCSP结构示意图
多芯片封装技术将多个芯片在基板端互连,并进行封装。与单芯片分立技术相比,采用多芯片封装技术可使芯片间距离更近,连接线更短,传输延迟大大降低。多芯片封装结构根据芯片间信号互连方式又可以分为焊线互连封装结构、倒装互连封装结构、焊线和倒装混合互连封装结构。
在进行系统级封装设计时,需要充分考虑芯片到芯片、芯片到元器件、元器件到元器件之间的距离,布局时尽量将这些间距缩小。此外,在进行基板线路设计时选择更细的线宽和更小的线距,也可以进一步提高封装的集成度,缩小整体封装体的尺寸。排版布局设计示意图如图3-36所示。
2. 2.5D高密度结构设计(2.5D High Density Structure Design)
与2D高密度结构不同,2.5D高密度结构通常采用转接板(Interposer)来实现更高密度的互连。图3-37所示为2D高密度结构与2.5D高密度结构对比图。

图3-36 排版布局设计示意图

图3-37 2D高密度结构与2.5D高密度结构对比图
从结构上看,转接板位于芯片和基板中间,起到连接芯片和基板的作用;从电性能上看,转接板起到转移导通的作用。转接板需要具有良好的综合性能,包括高电阻率、低损耗、高导热性、热膨胀系数和硅热膨胀系数相匹配、高强度、高模量、通孔易成型、成本可控。根据所用的材料,转接板可以细分为玻璃转接板、硅转接板、有机转接板。相比于其他材质的转接板,玻璃转接板的过孔等加工处理并不占优势,但其材料性能较好、成本较低。不同型号玻璃转接板的热膨胀系数表现有所差异。例如,Pyrex玻璃转接板的热膨胀系数与硅热膨胀系数近乎匹配,在一定程度上可以减少加热过程中产品的形变问题。不同类别转接板的热性能对比图如图3-38所示。

图3-38 不同类别转接板的热性能对比图
与硅转接板相比,玻璃转接板的S参数损耗更小,电性能较优,如图3-39所示。

图3-39 玻璃转接板和硅转接板电性能对比图
随着孔径的变大,玻璃转接板S参数的损耗更大,如图3-40所示。

图3-40 玻璃转接板不同通孔半径S参数损耗
若要在2.5D封装体中实现高密度设计,则需要在转接板上采用更小的间距和通孔,并缩小芯片与芯片之间的距离。2.5D封装结构图如图3-41所示。

图3-41 2.5D封装结构图
不同供应商的制程能力存在一定差异,玻璃转接板供应商的加工能力如表3-2所示。
表3-2 玻璃转接板供应商的加工能力

3. 3D高密度结构设计(3D High Density Structure Design)
为了追求更小的产品面积,采用将芯片进行纵向堆叠的方式,从而形成了3D封装。3D封装能够堆叠不同类型的多种芯片,在一定高度下,保证尽可能小的封装面积,在处理器、内存芯片等领域获得了广泛应用。
(1)硅通孔(TSV)互连。
TSV技术是一种在芯片之间通过TSV工艺进行互连的技术,能有效缩短互连长度,最小化封装尺寸,改善电性能。目前TSV主要有两种加工技术:一是离子刻蚀;二是激光打孔。通孔按照加工时间可分为先通孔(Via First)和后通孔(Via Last)两种。先通孔在晶圆制造过程中实现,后通孔在封装厂实现。
图3-42为电镀铜TSV填孔与熔融锡TSV填孔加工流程对比图。
通孔填充是TSV制造的重要工序之一,传统的实现方式是电镀铜填孔,还可以通过熔融锡完成通孔填充。电镀铜是目前研究最多、应用最成熟的工艺,缺点是比较费时。TSV的具体制作工艺将在6.5节详细介绍,这里不再深入描述。
相比采用焊线工艺的3D封装,采用TSV工艺实现的3D封装极大提高了基板的利用率,缩小了封装尺寸,具有更优异的电性能、更好的散热性、更高的集成度。采用TSV工艺3D封装密度的高低主要由TSV的孔径和孔间距决定,在相同I/O端口数量的情况下,孔径和孔间距越小,密度越高,集成度也越高。采用TVS工艺的3D封装结构如图3-43所示。

图3-42 电镀铜TSV填孔与熔融锡TSV填孔加工流程对比图

图3-43 采用TSV工艺的3D封装结构
(2)芯片堆叠互连。
芯片堆叠(Stack Die)封装结构可分为金字塔形芯片堆叠结构、倒金字塔形芯片堆叠结构;根据芯片间信号互连方式不同又可以分为焊线互连芯片堆叠结构、倒装互连芯片堆叠结构、焊线和倒装混合互连芯片堆叠结构这三大类,分别如图3-44~图3-48所示。
(3)芯片-晶圆键合(Chip to Wafer Bonding,C2W)互连和晶圆-晶圆键合(Wafer to Wafer Bonding,W2W)互连。
芯片-晶圆键合将单个芯片倒装到晶圆上后再切割成单个产品。晶圆-晶圆键合将整个晶圆倒装互连后,再切割成单个产品,如图3-49所示。

图3-44 金字塔形芯片堆叠结构

图3-45 倒金字塔形芯片堆叠结构

图3-46 焊线互连芯片堆叠结构

图3-47 倒装互连芯片堆叠结构

图3-48 焊线和倒装混合互连芯片堆叠结构

图3-49 芯片-晶圆键合和晶圆-晶圆键合互连方式示意图
芯片-晶圆键合互连与晶圆-晶圆键合互连的优缺点对比如表3-3所示。
表3-3 芯片-晶圆键合互连与晶圆-晶圆键合互连的优缺点对比

高密度封装往往不局限于单种封装技术,很多应用场景都会将基于转接板封装与基于TSV工艺的3D封装技术结合,整合不同类型芯片,用更小的空间实现更强大的功能,在系统级封装中得到了广泛应用。在TSV工艺下,逻辑芯片负责连接上下的影像传感器(CMOS Image Sensor,CIS)、模拟和射频芯片,硅转接板通过锡球实现芯片到基板的互连。与传统封装技术相比,3D封装技术能够实现更高密度的结构,更短的信号传输路径,电性能、热性能均表现优异。图3-50所示为多功能3D混合结构图。

图3-50 多功能3D混合结构图
4. 埋入式高密度结构设计
主流封装产品主要将芯片、无源元器件等贴装在基板表面后进行塑封,产品尺寸和厚度主要由塑封体的内部空间决定。
在产品小型化的发展趋势下,以智能手机为代表的便携式通信产品和可穿戴产品对封装产品提出了更小、更薄、更轻的需求。在这种背景下,埋入式封装结构应运而生。通过将芯片、无源元器件嵌入基板内部,可以把基板内部空间充分利用起来,不仅可以大大节约基板表面空间,还可以消除焊接点,减少引入的电感量,从而降低电源系统的阻抗。这样不仅可以将封装产品做得更小、更薄,可靠性、电气性能也得到了一定程度的提高。
埋入式高密度结构可以分为平面埋入式结构和分立式埋入结构两大类。
(1)平面埋入式结构设计。
平面埋入式结构对电容、电阻、电感埋入时的设计要求不同。埋入式电容技术会在PCB上建立一个大的平行板极电容。基板采用埋入式电容工艺的结构如图3-51所示。
所得电容量的大小取决于绝缘层厚度、介电常数、PCB尺寸,计算公式为
C=ADkK/t
式中,C为电容量,A为面积,Dk为介电常数,K为常数,t为厚度。

图3-51 基板采用埋入式电容工艺的结构
因此,当材料选定后,Dk和K就已经确定,电容量C仅与面积A和厚度t有关系,当把电容埋入基板,叠层结构也定下来后,电容量就由铜箔的面积决定,可以设计不同的形状、尺寸、面积,以满足不同电容量的要求。图3-52所示为埋入式电容结构图,采用的是圆形。

图3-52 埋入式电容结构图
埋入电阻可以采用平面减成法,将电阻铜箔直接压在基板层,通过蚀刻的方法将电阻加工出来,如图3-53所示。
埋入电阻还可以采用平面加成法,将电阻浆料直接印刷在基板线路层,如图3-54所示。

图3-53 采用平面减成法埋入电阻示意图

图3-54 采用平面加成法埋入电阻示意图
电阻值R的大小取决于材料的电阻率ρ、截面积S和长度L,计算公式为
R=ρL/S
通过设计不同长度和不同截面积的线路,可以得到不同的电阻值。一般会将线路设计成直线、S形、L形、弯折形等,设计非常灵活,可以实现高密度集成的埋入式电阻设计方案,进一步提升空间利用率。不同埋入式电阻图形的设计如图3-55所示。

图3-55 不同埋入式电阻图形的设计
(2)分立式埋入结构设计。
分立式埋入结构主要可以埋入无源元器件和芯片。在埋入成品电阻、电容、电感等无源元器件或芯片时,需要考虑所选元器件的尺寸、厚度(这些参数会影响埋入后基板的尺寸和厚度)。分立式埋入无源元器件切片结构图如图3-56所示。分立式埋入芯片切片结构图如图3-57所示。

图3-56 分立式埋入无源元器件切片结构图

图3-57 分立式埋入芯片切片结构图
在设计分立式埋入结构时,可以参考相关规则进行排版设计,以便实现高密度结构的需求,最大限度地将基板内部空间利用起来。分立式埋入无源元器件结构设计规则如图3-58所示。分立式埋入芯片结构设计规则如图3-59所示。

图3-58 分立式埋入无源元器件结构设计规则

图3-59 分立式埋入芯片结构设计规则
根据分立式埋入结构的原理,可以将原有WLCSP芯片贴装在基板之上的方式更改为芯片埋入基板内,这种设计方式可以极大地缩小系统级封装的尺寸,可以进一步提升电性能、可靠性和散热性,如图3-60所示。

图3-60 将WLCSP芯片贴装在基板之上的方式更改为芯片埋入基板内的示意图
(3)平面埋入和分立式埋入混合的结构设计。
由于平面埋入和分立式埋入都有各自的优缺点和限制,因此在一些应用中,会将这两种方式结合起来,最大程度地利用这两种方式的优点,使产品的集成度更高。例如,将平面埋入式结构与分立式埋入结构结合起来,采用平面埋入方法将高电感和电容填入基板中,并用分立式埋入方法将大容量电感埋入基板中,从而大幅缩小单个产品的尺寸,提高设计的密度。在此设计基础上,如果将芯片也埋入基板中,那么可利用的空间会更大,密度更高,如图3-61所示。

图3-61 平面及立体混合埋入式基板结构示意图
综上所述,灵活地采用不同的埋入式设计组合,可以使产品的集成度更高、尺寸更小、可靠性更高、散热性能更好。