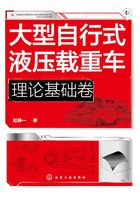
第三节 模块车整体结构设计
自行式模块轴线运输车是在普通牵引平板车的基础上,随着液压技术的发展而出现的一种自行式、可装卸的高端产品。这种多轴线运输车和动力平板车一样,不需要牵引车牵引,可以实现自行驶功能。它主要由两部分组成:动力模块单元(PPU)及带驱动的轴线模块单元(承载单元)。其中动力模块单元为整部车提供动力。而轴线模块单元作为承载单元,主要起承载运输货物的作用,多个承载单元可以实现串并联拼车工作。模块车的工作环境如下:
① 环境温度 最高气温40℃,最低气温-20℃。
② 环境湿度 最大相对湿度95%。
③ 工作风级 小于等于六级。
图3⁃9所示为模块车的整车结构图。

图3⁃9 模块车整车结构图
1—动力单元;2—制动气室;3—悬挂机构;4—驱动轴线;5—转向机构;6—车架;7—从动轴线
一、模块车动力单元设计
模块轴线运输车的动力单元位于车的最前端,整个动力单元长3085mm,宽2990mm,高850mm。动力单元与后边的承载单元用销轴铰接。另有两个对称布置的液压缸,在模块车爬坡时,根据坡度不同,调节这两个液压缸的伸缩量,使其推动动力单元提升一定的角度。发动机位于动力单元的中间位置,考虑到整车的高度限制,本车采用了奔驰的卧式发动机,功率为300kW。该发动机起步性能好,加速快,爬坡能力强,并且油耗小,比国内同类产品低20%,满足欧Ⅲ排放标准。闭式泵和开式泵通过分动箱连接到发动机上,分别为驱动马达和转向、悬挂液压缸提供动力。动力单元液压管路与承载单元液压管路通过快速接头连接,快速接头通过一个支架固定在液压油箱的上方,整个液压管路布置整洁、美观。动力单元的侧面挡板上开有散热孔,顶部有盖板盖着。另外液压油箱、燃油箱、液压冷却系统、电控柜以及气动控制阀等也安装在动力单元中。图3⁃10为模块车动力单元的布置图,相关技术参数见表3⁃3。

图3⁃10 模块车动力单元布置图
1—冷却器;2—电控柜;3—气动阀;4—发动机;5—燃油箱;6—闭式泵;7—开式泵;8—液压油箱
表3⁃3 模块车动力单元技术参数

二、模块车承载单元设计
表3⁃4所示为模块车承载单元的技术参数。
表3⁃4 模块车承载单元技术参数

模块车承载单元长9440mm,宽3000mm,重34t,总共有六个轴线,中间四个轴线为驱动轴,驱动车桥里装有马达减速器,为整车行走提供动力。边上两个轴线为从动轴,安装有制动气室,实现模块车的驻车制动和紧急制动。
承载单元采用纵横网格加强型轴线车架。车架下面自顶向下依次安装有转向液压缸、转向臂、悬挂架、悬挂柱塞缸、平衡臂、驱动/从动桥、轮胎。整个承载单元呈前后、左右对称布置,外形美观,承载均匀。车架、悬挂机构等主要承载构件采用了Q690高强度低合金结构钢,使得车在相同负载下重量更轻,大大提高了其机动性能。车架主梁高度约为700mm,位于车辆中心轴线上,为整体式无焊接工字梁,具有很好的抗弯、抗扭能力。副梁采用高强度钢焊接而成,与主梁一起构成模块车的承载结构架。
三、模块式液压运输车车架机械结构分析
图3⁃11所示为模块式运输车车架结构图。模块车额定载荷200t,车架全长9.3m,宽3m,高0.7m,轴距1.55m,为鱼骨式结构。模块车车架由主梁、副梁、横梁、斜支撑、连接架、端梁等焊接而成,其中主梁、副梁、横梁为焊接式箱型梁结构。

图3⁃11 模块式运输车车架结构图
1—主梁;2—副梁;3—横梁;4—斜支撑;5—连接架;6—端梁
模块车车架的结构较为复杂,在满足车架主要力学特征的条件下,为加快网格划分速度,控制求解的规模,保证模型划分网格时单元的质量和数量,有必要对模块车车架进行适量简化。根据前面所述有限元模型简化原则,对模块车车架进行了如下简化:
① 除去模型上承载力很小的构件和非承载构件,如车架两边盖板、斜支撑旁盖板、快换接头连接架等;
② 除去车架与液压悬架连接处的螺栓孔以及车架上的一些倒圆角等。
车架简化后的三维实体模型如图3⁃12所示。

图3⁃12 简化后的模块式液压运输车车架有限元模型
四、模块式液压运输车车架机械结构的静态分析
所谓结构静态分析,是指结构在固定不变的载荷作用下计算结构对载荷的响应,它既不考虑阻尼和惯性对结构的影响,也不考虑载荷随时间的变化。通过对车架结构进行有限元静态分析,确定模块车车架各结构件在载荷作用下的应力、应变分布状况。设计人员可以校核车架是否满足各种工况下的强度、刚度要求,反过来,有限元分析结果作用于设计过程,可使零部件结构设计更加具有目的性,受力、质量分布更加合理。
结构强度有限元静态分析,使得设计人员对所设计的结构在每种工况所确定的载荷的作用下其结构的强度、刚度及稳定性情况有一个全面而准确的了解,根据计算所得到的结构上各处位移和应力的分布结果,结合相应的设计标准或规范,判断所设计的结构可靠性和经济性,在此基础上进行改进或优化设计,从而避免某些结构或零部件由于过大的应力或压曲失稳而损坏,并控制机械结构整体及其零部件的刚性性能。另外,对于那些所受应力较小、结构材料利用不充分的区域,可以结合加工和制造工艺的实际情况进行材料板厚减薄、截面尺寸减小等,从而达到降低成本的目的。
作为强度校核基准,以材料发生塑性变形作为材料失效的标准,因此可以按照第四强度理论对车架进行静态强度校核,选择Von Mises等效应力来校核车架结构的强度:
σr=(3⁃1)
式中 σ1、σ2、σ3——第一、第二、第三主应力。
对模块车车架进行有限元分析,步骤如下:
① 定义分析类型 分析类型为Static Structural。
② 定义材料属性 整车采用Q690D结构件焊接而成,Q690D各项性能参数如表3⁃5所示。
表3⁃5 Q690D材料属性

由强度条件可知:
σr≤≤
=345(MPa)(3⁃2)
式中 [σ]——材料的许用应力,MPa;
n——安全系数,此处取2。
③ 划分网格 采用智能化网格划分方法,由于六面体网格单元具有求解精度高、所需网格单元数量少等优点,因此整车网格单元网格类型设定为六面体网格单元。车架网格划分结果如图3⁃13所示。

图3⁃13 模块式液压运输车车架有限元网格划分示意图
④ 施加约束、载荷
a.约束处理。根据实际中载重运输车载重后的受力分析,对第二轴与第五轴悬挂处进行全约束,其他四轴约束悬挂处x、z方向平动位移。
b.载荷处理。
模块车自重:设重力加速度为9.8m/s2,ANSYS Workbench会根据材料属性里设定的材料密度、整车的体积自动计算出整车的自重。
模块车额定载荷:模块车的额定载荷为200t,根据模块车运输物件的实际情况,加载工况分两种,如图3⁃14所示。

图3⁃14 模块车主要加载工况
均布加载,即模块车承受的载荷均匀分布在整个车架上。当运输物件较为规则,可直接将物件置于车辆之上,此种加载方式即为均布加载,如在运输大型船舶分段时即可视为此种加载方式。
模块车第二、第五轴线处集中加载。当模块车运输大型圆柱状物件时,其运输方式为先将两个半圆形钢架支撑架构置于模块车上,再将货物置于两个半圆形钢架支撑架构上,以实现货物的运输,如运输大型石化设备蒸馏塔即为此种加载方式。
因此,模块车两种加载工况下有限元模型的约束受力图如图3⁃15所示。

图3⁃15 两种加载方式下的约束受力图
⑤ 求解、分析 经过ANSYS Workbench求解,分别得到模块车在两种不同加载方式下车架的等效应力云图Equivalent(Von Mises)Stress和位移变形云图Total Deformation。图3⁃16所示为均布加载下的等效应力云图和位移变形云图;图3⁃17所示为第二、第五轴线处集中加载下的等效应力云图和位移变形云图。

图3⁃16 均布加载下的等效应力和位移变形云图

图3⁃17 第二、第五轴线处集中加载下的等效应力和位移变形云图
图3⁃17中,工况(a)加载条件下,其最大应力为218MPa,位于第二、第五轴线处模块车车架与悬挂连接处,小于材料的屈服极限,其他部位应力大约为48MPa以下,因此满足材料许用应力。最大位移量为10mm,出现在车架端部,但变形量相对于整车长度来说比较低。可以看出,工况(a)加载条件下的模块车车架除了几个局部位置出现应力集中外,整车其余部位的应力水平并不高,其变形量相对也较低,因此材料并未得到充分利用。
工况(b)加载条件下,其最大应力为271MPa,位于第二、第五轴线处模块车车架与悬挂连接处,小于材料的屈服极限,其他部位应力大约为60MPa以下,因此满足材料许用应力。最大位移量为9mm,出现在车架端部,但变形量相对于整车长度来说比较低。可以看出,工况(b)加载条件下的模块车车架除了几个局部位置出现应力集中外,整车其余部位的应力水平并不高,其变形量相对也较低,因此材料并未得到充分利用。
由于在分析中没有考虑焊缝对应力应变结果的影响,而在实际中平滑弧形焊缝有利于减小应力集中现象,因此分析的应力结果可能比实际有所提高。除以上应力集中外,模块车其余大部分部位的应力水平较低,强度富余量比较大,材料并未得到充分利用。因此,在满足车架强度的条件下,可以考虑对模块车车架结构进行减重改进,减轻模块车整车的重量,从而提高模块车材料质量利用系数。
五、模块式液压运输车车架机械结构的模态分析
模态作为结构振动系统特性的一种突出的表现形式,通过模态分析便可得到结构的固有频率和主要振型,而固有频率和振型是评价结构动态设计性能的重要性能指标,能为振动系统动态设计提供理论依据。模块车车架为一弹性系统,由于外界的激励将使整车产生振动响应。当模块车车架的固有频率与外界激振频率接近时,车架很可能会产生共振,共振则会导致车架上的某些部位产生数值很大的共振动载荷,致使车架各部件产生疲劳损坏,缩减车架及整车的使用寿命,威胁车辆的使用安全。因此,为保证车架具有良好的动态特性,要求车架的固有频率和振型应该避开常见的激振频率,故在车架设计的阶段,对车架进行模态分析是很有必要的。由振动理论可知,结构的动态特性主要由低阶振型所决定,高阶振型即使产生其能量相对来说也比较小,所以模态分析一般取5至10阶精度就已满足要求。本文重点分析模块车的前六阶振动特性。
模块车车架模态分析与静态分析相类似。其分析类型定义为Modal,材料为Q690D,网格划分、约束与静态分析相同。由于结构的振动特性是由结构本身特性所决定的,与所受载荷无关,因此结构模态分析不需要施加载荷。
通过ANSYS Workbench求解得到模块车车架结构的固有频率与振型。表3⁃6所示为模块车车架结构前六阶振动频率,图3⁃18所示为相对应的前六阶振型,通过振型云图可以非常直观地识别车架在不同频率时的振动趋势。仿真结果用不同颜色直观地标识出模块车车架各部分结构振动的强弱分布以及抗振薄弱区,为模块车车架结构优化设计提供了参照依据。
表3⁃6 模块车车架结构前六阶振动频率


图3⁃18


图3⁃18 模块车车架前六阶模态振型图
模块车车架主要受到发动机和路面的双重激励作用。
① 发动机激励频率f1:
f1=(3⁃3)
式中 n——发动机转速,r/min;
z——发动机气缸数;
τ——发动机冲程。
模块车所用发动机为水平卧式6缸4冲程发动机。怠速时发动机转速为(600±50)r/min,发动机的振动频率为(30±2.5)Hz;常用转速为1100~2000r/min,发动机振动频率为55~100Hz。
② 路面激励频率:
f2=(3⁃4)
式中 v——车辆行驶速度,km/h;
λ——路面不平度波长,m。
由于模块车大多数工况下处于公路作业状态,路面不平度波长范围为1~6.3m,因此由路面不平度所带来的振动频率范围为1.6~10Hz。
由表3⁃6分析可知,车架的前6阶模态中:①第1阶和第2阶振动频率低于发动机怠速激励频率,且远大于路面激励频率,此时车架不会与发动机、路面产生共振;②第3阶至第6阶固有频率,大于发动机怠速激励频率,且低于发动机常用转速激励频率,此时车架仍不会与发动机产生共振。所以车架的设计完全符合振动特性要求。