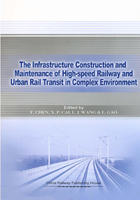
RESEARCH OF SUBWAY TRACK PARAMETERS BASED ON VIBRATION CONTROL
Hua PENG,Xiaoyun LIU,Xiaopei CAI,Wenhui MA
School of Civil Engineering,Beijing Jiaotong University,Beijing 100044
Abstract:In order to reduce the impact of noise and vibration caused by subway operating on the surrounding environment,kinds of vibration of subway track structure was introduced,but as for the lack of operating experience and experimental data,subway track design is not parameterized enough,which results in especially in the rail dampers fastening rail lines a serious rail corrugation.Comparing the subway lines which are abnormal corrugation and not,finding the track stiffness especially bearing stiffness values are quite different;in addition the fastening space affects the track structural strength,stability and deformation,and it also has a significant impact on the track structure stiffness.Taking abnormal rail corrugation as a starting point,to research bearing stiffness,fastening space and bearing damping especially on the rail abnormal corrugation,analyze the effects of different parameters on the track mode,the wheel-rail dynamics properties,subjecting to a goal which avoids resonance furthest.
Keywords:subway track structure,parameters,fastening stiffness,fastening space,damping
Email:hpeng@bjtu.edu.cn
1 Introduction
Urban rail transit is at a high speed of development,the rapid development of rail transportation network gives the citizens convenience to travel,while it caused certain environment problem as vibration and noise.In recent years,abnormal corrugation appeared in some damping track sections,when the train travels through the rail corrugation sections,the wheel/rail contact stresses will be enlarged.This will not only damage the durability of the track structure,also cause the noise pollution that cannot be ignored.In Beijing,subway track in the damping section has a rapid development of rail corrugation,and accordingly its rail grinding period is short.This situation is found both in straight and curve line.The appearance and development of corrugation has close relation with the wheel/rail resonance,furthermore,when the corrugation has appeared,it is more advantageous to filter and amplify the wheel/rail force related to the corrugation frequency,so as to further accelerate the development of corrugation.
Engineering structure vibration characteristic is mainly decided by quality distribution,stiffness distribution and damping characteristic.Reflecting in track structure is mainly decided by fastener’s stiffness,damping,and space.Thus,it should mainly embark from the optimization of the three parameters to control the vibration of track structure[1].
2 Theory for Control of Track Vibration
Through the analysis of the single degree of freedom system under harmonic excitation,get the amplitude of forced oscillation is:

When resonance occurs,the result will be gotten:
Bmax=F /2ζβk=F/ cpn (2)
among them,B is the amplitude of the forced vibration;F is the amplitude of the harmonic force;k is spring stiffness;β is the ratio of the harmonic frequency and the natural frequency of the structure;ζ is damping ratio;pnis Nstnatural frequency of the system.
From the two formulas above can be seen,the amplitude of forced vibration depends on the magnitude of excitation force,frequency ratio,damping ratio of the system,stiffness.On this basis,the main factors that control the vibration amplitude can be obtained.
(1)Decrease the amplitude of disturbance force.In the wheel/rail system it can be realized by decreasing train’s axle weight or improving quality distribution of the wheelset.In addition,improving the flat and comfort of the wheel/rail connecting surface also can decrease the peak of wheel/rail force.
(2)Change the ratio of the force’s frequency and the system’s natural frequency,putting the vibration in the non-resonant area,in order to reach the purpose of decreasing amplitude.By the Formula(1),when w=pn,vibration amplitude is maximum,while,the bigger of w-pn,the smaller of the amplitude,obviously.Changing the natural frequency of structure can be realized by changing stiffness k or quality m.Increasing or decreasing constraint,in other words,changing the space between the fasteners changes the natural frequency of the system.Changing the track’s distribution of quality and stillness affects natural frequency.Changing the track’s rigidity is to change its potential energy,and changing the structure’s quality is to change its kinetic energy.If the stiffness characteristic value of the track structure increases while the kinetic energy is constant,every orders frequency of the structure increases.If the quality distribution characteristic value of the track structure increases while the potential energy is constant,every orders frequency of the structure decreases.
(3)Add damping force to the engineering structures.Adding damping force to the engineering structures makes resonance amplitude and non-resonance amplitude reduced[2].
3 Wheelset and Track Structure Model
3.1 Wheelset structure model
Wheelset’s appearance is made according to the actual size of subway vehicle,with elastic modulus of 2.06×1011N/m2,Poisson ratio of 0.3,and density of 7850 kg/m3.Rigidity and damping ratio of the primary suspension used the practical design value.Use finite element software to make the entity model of the wheelset structure,that is regarding wheelset structure as elastomeric,as is shown in the Figure 1.

Figure 1 Finite element model of wheelset
Firstly,the modal analysis of the wheelset is carried out,getting its natural frequency and vibration type in range of 1000 Hz[3].
In the range of 1000 Hz,the natural frequency of wheelset structure is shown in the Table 1.
Table 1 Vibration type orders and corresponding frequency of wheelset


Figure 2 Order of wheelset and corresponding frequency distribution
After observing the modal analysis results of metro vehicle wheelset,it is found that the vibration of subway wheelset has some distribution rules in the range of 1000 Hz,the first 11th orders natural frequency distribution within 0-117 Hz,12th-14th orders distribution within the range of 283.99-311 Hz,after 15th order continuous distribution within the scope of the 454-1000 Hz.Thus,it shows that the natural frequency of subway cannot be in 120-283 Hz and 311-454 Hz.Therefore the selection of the parameters of subway track structure should try to make the main frequency distribute in the two zones,120-283 Hz and 283-311Hz.
Assuming that wheel and rail contact in the single point,unit harmonic force applied at the center of the wheel/rail contact spot,within the frequency range of 1000 Hz,getting the wheelset structure’s frequency response function curve.

Figure 3 Wheelset structure’s frequency response function curve
Peak area(30 Hz,60 Hz,65 Hz,110 Hz,110 Hz,472 Hz ,472 Hz)said wheelset occurs vertical resonance at the frequency,while wave trough(91 Hz,311 Hz,341 Hz,678 Hz)said that wheelset occurs vertical anti-resonance at the frequency.And whatever resonance and anti-resonance happened,the response of the wheelset decreased with increasing frequency.
The frequency mode in the peak area was analyzed detailed.Among them,the vibration mode of the wheelset affected by the vertical excitation with the frequency of 30 Hz is shownas Figure 3.

Figure 4 2ndorder vibration mode of wheelset
When the wheelset vibrates with the frequency of 30 Hz(the 2ndorder),it happened axisymmetric flexural vibration,with the biggest deformation in the axle center section,and along with the increase of the distance from the center the deformation decreases,and the deformation of the wheel for each location is relatively consistent,thus it can be seen in 30 Hz both the vibration shape and size probably cause the great vertical vibration of wheel/rail system.Thus the parameter setting needs to avoid the system from resonance at the frequency of 30 Hz.
The vibration mode of the wheelset affected by the vertical excitation with the frequency of 60 Hz is shown in the Figure 4.When the wheelset vibrates with the frequency of 60 Hz,it happened central symmetry anti-vibration,and along with the increase of the distance from the center the deformation increases.The entire deformation of the wheelset is vertical bending deformation,thus the vibration mode at 60 Hz will exacerbate the wheel/rail vertical resonance.The parameters design should avoid the vibration mode consistent with or close to the natural frequency.

Figure 5 5thorder vibration mode of wheelset
So it is clear that the natural frequency of wheelset structure is dispersed within the range of 0-1000 Hz,and is relatively uniformly distributed in some range,and there are some frequency band “disconnect” as wide as hundreds Hz.As a result,the design of subway track parameters needs to consider two principles.The first is to make use of frequency disconnect space,and the second is to make the frequency larger.In other words,try to avoid the natural frequency of the wheelset and make the resonance of the track and wheelset occur at the larger frequency.
The frequency gotten from the wheelset frequency response curve and from modal analysis cannot perfectly fit.The reason is that different modes have different contribution for the actual vibration.Overall,low frequencies contribute more to the vibration of the wheelset,and various vertical vibration deformations of wheelset occur at the 2nd,5thand 10thorder vibration mode.
3.2 Rail structure parameter analysis
In this paper,track model adopted by rail,fastener system,track plate and foundation.Rail is simplified to Timoshenko beam model.Track plate simplified finite element model for three-dimensional entities,with a linear spring damping fasteners unit simulation system.The connection between the bottom of the plate and the subgrade using equivalent spring damper unit simulation.
For rail modeling,closely related to the formation of a wave due to rail grinding and vibration,in this paper,we use the Timoshenko beam model to reflect the high frequency vibration,in addition,the model also consider the effect of rotary inertia and shear deformation.Timoshenko beam,relative to the Euler beam model can more accurately simulate vibration under various incentives,and more conducive to the analysis of the causes and mechanism of wave rail grinding.Under the implementation process of numerical,the steel is processed into finite long Timoshenko beam.When orbit calculation length is long enough,the influence of the simply supported on both ends will be small,which can satisfy the demand of precision.
Select different key parameters of track structure,in order to avoid or reduce the resonance parameters optimization target of track structure,and compared different key parameters of the track structure under the condition of dynamic characteristics and change rules.
In order to facilitate research,the study of parameters using the control variable method,namely,under the condition of other parameters are fixed to adjust parameters of track structure,as shown in Table 2,in which the calculated results were compared.
Table 2 Track structure parameter

According to Table 2 parameters combination condition,selection of 0.45 m,0.65 m,0.75 m,0.90 m four different bearing spacing situation has carried on the modal analysis of track structure,and get the modal parameters:modal vibration mode and natural frequency.
The Figure 6 shows that under the condition of changing track structure bearing spacing,inherent frequency of the track structure changes,because the change of bearing spacing can change the constraint condition between stiffness distribution of track structure and components.Increasing the bearing spacing,rail support conditions will become soft,which will cause the overall elastic strength.From the view of engineering finite element,changing bearing spacing is equal to the change of track structure stiffness matrix,and the stiffness matrix of eigenvalues have smaller trends.As we can see from the diagram,especially in the high-level modes,with the increase of bearing spacing,the high order frequency of the track structure can have a significantly lower.

Figure 6 Modal parameters of different supporting spacing
Using 0.45 m,0.65 m,0.75 m,0.90 m four different supports spacing to analyze the harmonic response of track structure.

Figure 7 Track structure dynamic response of different spacing bearing
Observation analysis Figure 7,the harmonic load within the range of 0-1000 Hz,under the action of four kinds of working condition of bearing spacing there were multiple resonance peak,and the response is relatively strong peak are mainly distributed in the range of 0-300 Hz range.Therefore,in the range of support spacing from 0.45 m to 0.90 m ,the main vibration frequency track structure can’t be more than 300 Hz,but change in supporting spacing waveform integral will happen to a certain degree of mobile,and it is easy to see,increasing the bearing spacing can make the peaks move to the left.Observing and analyzing the ordinate of frequency response function can be learned,under two kinds of working condition 0.75 m and 0.90 m,a strong response is appeared in about 50 Hz and 80 Hz.Therefore,increasing the bearing span 0.75-0.90m interval range is likely to lead to track structure caused by occurs due to the low frequency resonance and instability.From this point of view,supporting spacing should be controlled in the smaller range.
According to Table 2 parameters combination condition,select 10 kN/mm,20 kN/mm,30 kN/mm,40 kN/mm,50 kN/mm five different bearing stiffness cases to analyze the frequency response of track structure,frequency response function under the condition of the five kinds of operating modes are here.

Figure 8 Track structure dynamic response of different bearing stiffness
According to comparative analysis of five kinds of operating modes,maximum of the frequency response function is the maximum of 50 kN/mm frequency response function curve.Therefore,the track structure under the condition of 30 kN/mm responses is strongest.The minimum is obtained under the condition 10 kN/mm.
According to Table 2 parameters combination condition,selection of 1.5 kN·s/m,4.0 kN·s/m,6.5 kN·s/m,9.0 kN·s/m,50 kN/mm five different bearing damping cases to analyze the frequency response of track structure,condition of frequency response function under the five kinds of operating modes are obtained.

Figure 9 Track structure dynamic response of different bearing damping
Within 0-70 Hz,the change of bearing damping does not cause the rail response to a big change,which suggests that in low frequency force changing the bearing damping have little impact on the vibration characteristics of track structure.Within 70-370 Hz,there are mainly four main resonance peaks of different intensity of the frequency response function damping values of rail.Obviously track structure in the lower bearing damping value of 1.5 kN·s/m,the peak of rail frequency response function is higher than that of other state values.The reason is that bearing viscous damping the vibration characteristics of track structure affect mainly through damping ratio.
Thus,the influence of damping to the vibration characteristics of track structure is not linear,and selecting the high damping effectively reduces the vibration of the rail.
4 Conclusions
(1)According to the second quarter,from the perspective of avoiding resonance or reduce resonance,fastener spacing to change the modal effect of track structure is not very significant.Therefore,hoping that changing the bearing spacing is not ideal method to avoid the resonance,but increasing the bearing spacing can lead to quick response of rail,may lead to instability of track structure.All in all,the fastener spacing should keep the original design parameters.
(2)Fastener stiffness get the peak value of vibration response at 50 kN/mm,fastener stiffness to the influence of the vibration characteristics of track structure is roughly linear,the low stiffness can effectively reduce the intensity of rail response,but lead to buckle on the wheel-rail force transfer effect is poorer,this is to say that rail can appear in the formant amplitude is obviously superior to the bed board of vibration,which may accelerate the production of rail grinding wave,at the same time can reduce the durability of fasteners.And when choosing low stiffness we must ensure that the damping is sufficiently large.
(3)Increase bearing damping can effectively reduce the resonance and the non-resonance amplitude values.In the practical application of the fasteners,DTVI2 fastener has larger damping,application status are good.absorber fasteners has low stiffness and damping,so in practice it appears serious corrugation.
References
[1]Li K.F.,2012.Based on the Subway Tracks Shift and Damping Force Characteristic Curve Rail Coupling Frequency Domain Analytical Model Study[D].Beijing:Beijing Jiaotong University.
[2]Li X.,2012.Study Metro Rail Corrugation Forming Mechanism[D].Chengdu:Southwest Jiaotong University.
[3]Gu A.J.,2011.Effect of Metro Rail Fastener Stiffness and Damping of Abnormal Corrugation[J].Urban Rail Transit,23(4):17-21.
[4]Xu H.J.,2014.Relationship Metro Small Radius Curve Section of Rail Track Stiffness and Abnormal Corrugation[D].Beijing:Beijing Jiaotong University.
[5]Li K.F.,Liu W.M.,2010.Metro Rail Corrugation Analysis[J].Urban Rail Transit,2:1-6.
[6]Guo J.P.,2011.Beijing Metro Line 4 Rail Corrugation Anomaly Investigation and Treatment Measures[J].Urban Rail Transit,24(3):10-13.
ICRE2016-International Conference on Railway Engineering